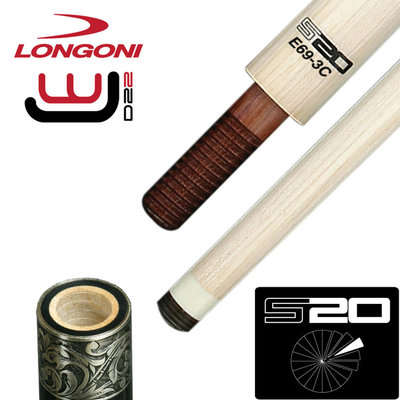
Longoni top end S20 carom 71 cm
This shaft was developed exclusively for the carom game, in close collaboration with Marco Zanetti, and is the first in the world with a structure of 20 cuts of hard maple from Quebec, which makes the shaft truly innovative. The game is easy and natural a
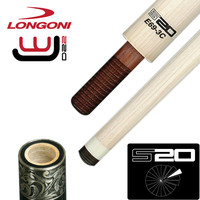
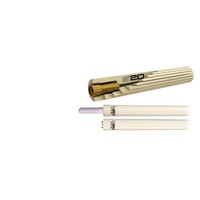
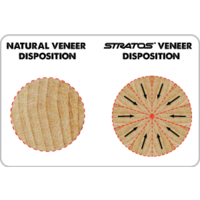
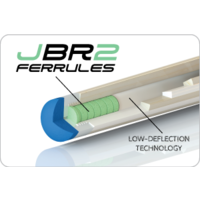
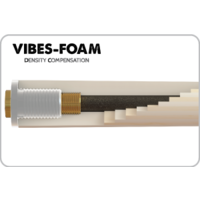
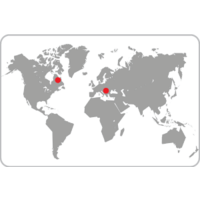
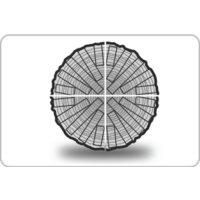
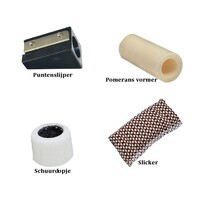
Longoni top end S20 carom 71 cm
Article code: 105290
0 reviewsadd your review
€328,55
Delivery time: This is currently not available. Choose another variant.
This shaft was developed exclusively for the carom game, in close collaboration with Marco Zanetti, and is the first in the world with a structure of 20 cuts of hard maple from Quebec, which makes the shaft truly innovative. The game is easy and natural a
More info
Product description
- Brand: LONGONI
- Article code: 105290
- Availability: Out of stock
- Delivery time: This is currently not available. Choose another variant.
![]() | THE CONCEPT OF STRATOS Wooden classical shafts are highly anisotropic and release uncontrollable forces during a hit. Renzo Longoni analyzed the problem in depth in the late 1960s and came to the conclusion that nature must be recreated. He decided to cut slices of wood, selecting them by weight, pure veneer and quality to create a perfect shaft using only the best pieces. Laminated shaft was born and patented in 1985. |
![]() | JBR2 FERRULE, G10 CORE AND LD TECHNOLOGY Constantly improving the quality of the game is one of the main goals of the Longoni team. To ensure the maximum playing performance of the Longoni shafts, we have worked extensively on their front end by introducing Longoni's new JBR2 ferrules with high-density G10 support and a proprietary system to reduce deflection and improve acoustics. |
![]() | VIBES FOAM To improve balance and acoustics, we made a long hole filled with a special foam in all laminated shafts close to the joint area. This material compensates for density, absorbs vibrations and improves balance. |
![]() | THE RIGHT PLACE FOR THE RIGHT WOOD This point is crucial: Stradivari was used to search for the best wood in the Panaveggio valley, where spruces grew in a microclimate unique in the world. The Longoni company uses only the best hard rock maple from Quebec (Canda) and the whitest European hornbeam for its shafts, where extremely low temperatures, sunlight and soil provide the best quality wood for billiards. |
![]() | CUTTING PROCESS The cutting of the trunks is done during the coldest periods of the year to obtain the best physical characteristics and that white color that distinguishes the best shafts: the Longoni shafts. From the central parts of the boards are taken the elements that must have straight and thick holes without the presence of knots or other aesthetic imperfections, including the sugar strips that can cause stains typical of the Saccharum maple. |
![]() | DRYING PROCESS The drying process starts when you cut the trunk into planks and leave them in the open air, in the extremely dry and freezing climate in which they are grown. Once the elements are removed from the planks, they are vacuum dried to mechanically remove most of the water retained by the cells. After the first run, all Longoni shafts are left in a special air-conditioned and constant drying room for at least a year to completely remove the last traces of moisture before proceeding with the stabilization process. |
![]() | STABILIZATION PROCESS Stabilizing the wood is the process whereby the wood, from a fully dried material, begins to absorb the natural environmental moisture to achieve the correct balance with the outside world. Thanks to this process, which takes at least 3 months after the drying chamber process, the shafts remain stable over time and ensure excellent playability. |
![]() | MAKING A LAMINATED SHAFT To make a laminated shaft, after properly drying and stabilizing the raw material, the wood must be cut into slices, which must be selected and glued with a combination of slow-setting adhesives. Gluing the laminated axles takes a lot of time: for the right result it is necessary to leave the glued slices in special molds for at least 24 hours. This technique significantly limits production capacity, but greatly increases the quality of the ash. |
![]() | S2, S20, S30... WHAT'S THE DIFFERENCE? S2 has 10 highly selected Canadian hard rock maple slices. An elastic shaft with determination, perfect for the most extreme English. S20 is the first in the world with a structure of 20 slices of Quebec hard rock maple, which makes the shaft truly innovative. The game is easy and natural and the deflection is completely cleared.
Thanks to the internal structure, the weight is well balanced. S30 is the last Stratos: 10 slices of Canadian hard maple combined with 10 slices of balcan hornbeam. Made for the player who likes strong, stable and higher density. |
![]() | STRATOS LONGONI WARRANTY All Stratos axles are uniquely numbered to track production date. Each shaft is also labeled to state the product specification, including code, name, diameter and exact weight. The label, in addition to showing these details, is a further guarantee of authenticity. Before labeling, each shaft is checked individually on a test table to prevent warping and other defects. To report the correct weight and diameter, we use a precision digital scale connected to the system and a laser micrometer. |
![]() | MADE WITH THE WORLD CHAMPIONS Longoni team players play an important role in the development of our shafts, as the skills of the best talent around the world allow us to create outstanding shafts. All our models have been tested and approved by our champions to guarantee the maximum results and satisfaction for our customers. The results speak for themselves: our shafts have won the most important world-class titles. |
![]() | MADE IN ITALY: YESTERDAY, TODAY AND TOMORROW All Longoni axles, including the laminated ones, are completely and uniquely produced in Italy at the factory in Mariano Comense with techniques and machines developed by us. The processing cycle of each shaft lasts a minimum of 24 months: from the moment you cut the board to the moment it reaches billiard tables around the world. The choice to continue manufacturing entirely in Italy was motivated by the desire to have a product different from all others in terms of quality and technology, always under the strict control of our staff. |
![]() | STRATOS SHAFT: PRECISION AND TRACEABILITY All Stratos axles are uniquely numbered to track production date. Each shaft is also labeled to state the product specification, including code, name, diameter and exact weight. The label, in addition to showing these details, is a further guarantee of authenticity. Before labeling, each shaft is checked individually on a test table to prevent warping and other defects. To report the correct weight and diameter, we use a precision digital scale connected to the system and a laser micrometer. |
Reviews